Reloading: Seating and Crimping Bullets
Tom McHale 04.15.14
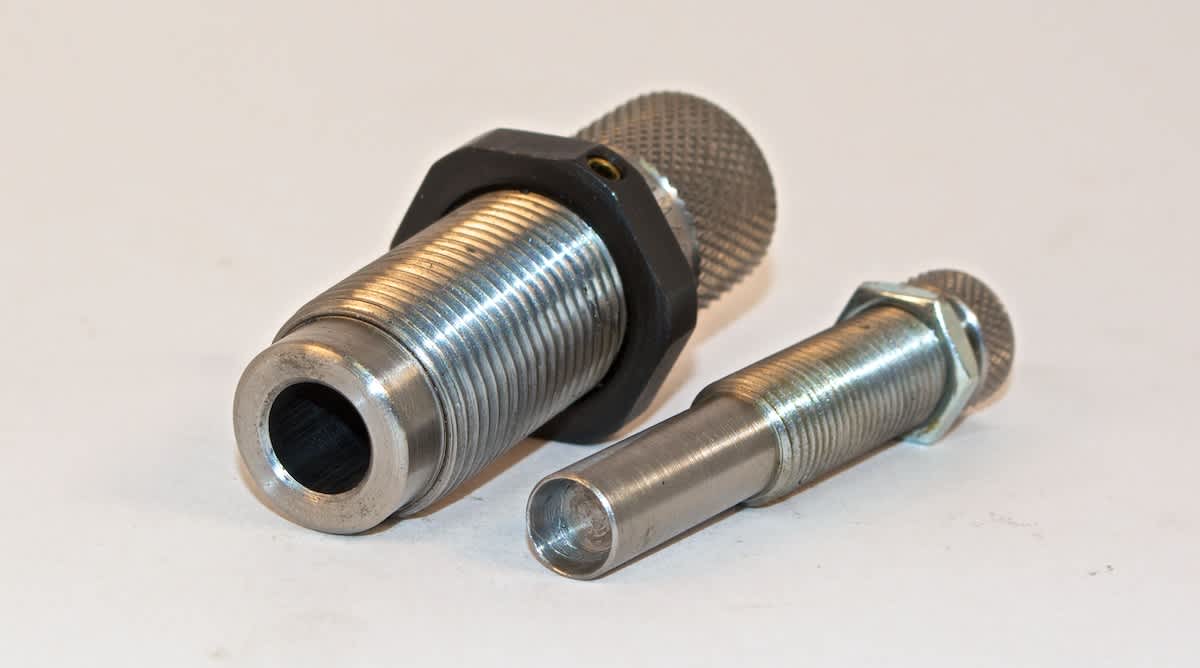
Last time we covered the powder charging step of reloading and briefly touched on the whole concept of pressure curves. While reloading is a safe pastime when proper care is taken, the care-taking part is a really big deal. The last steps—seating, crimping, and inspecting cartridges—are equally important when it comes to safety.
Seating the new bullet
Seating the bullet simply means pressing it into the cartridge case to the proper depth. Precise seating depth is important for a number of reasons. Obviously, the cartridge has to fit in the magazine and/or cylinder and chamber. Far more importantly, the seating depth has a big impact on peak pressure when the cartridge is ignited.
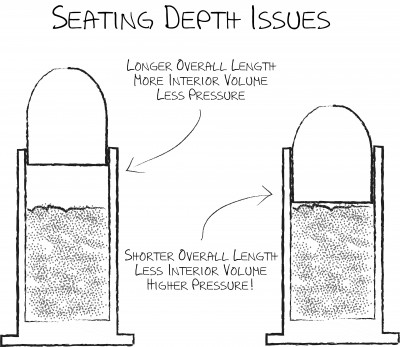
A cartridge overall length (COAL or COL) is specified for each type and weight of a bullet as a way to control the interior volume of the cartridge case. Any given published load recipe is carefully developed with an assumption about volume in the cartridge case. If a bullet is pushed farther into the case, there is less interior volume. If the same amount of powder ignites in a smaller volume, pressure will be have to be higher. Likewise, if a bullet is not pressed in deep enough, there will be more available volume in the case, and pressure will be lower.
Most seating dies actually perform two functions: seating and crimping. If you adjust your die and press exactly right, then you can do both steps at once with good reliability.
I prefer treating these as separate steps—especially for the new reloader. Here’s why: seating the bullet involves pressing it into the cartridge case. When you’re crimping at the same time, you’re applying inward pressure while also applying downward pressure, so you’ve actually got two forces that have to be perfectly timed for a correct result. If small details like cartridge case length are out of whack just a bit, you can actually create bulges in the case which may prevent the cartridge from chambering properly.
Crimping the new bullet
Crimping can be a bit of a misnomer. It sounds like it’s the process of squeezing the bullet into place in the cartridge case, but it’s really not.
If previous steps are done correctly, there is no need to squash the brass against the seated bullet to “squeeze” the bullet firmly into place. Case neck tension is what holds the bullet in place. If previous steps are done right, then a seated bullet will be pretty secure on its own.
For most semiautomatic pistol cartridges, crimping simply refers to the process of removing the “flare” of the cartridge case mouth, which we created in the case mouth belling step. Case mouth belling simply means opening up the mouth of the cartridge case just a bit to allow room for a new bullet to be inserted. For straight-walled cartridges, the process of removing this small flare from the case mouth is known as taper crimping.
A straight-walled pistol cartridge requires a taper crimp because there must be a hard edge to the cartridge case mouth—that’s the part that butts up against the ridge in the chamber to position the cartridge in the right place. For example, if you apply a roll crimp to a 9x19mm cartridge, there is no “hard stop” and the cartridge will be able to move back and forth in the chamber. If it moves too far forward, the firing pin may not reach the primer with enough force to fire the cartridge. Or, if there is too much space between the base of the cartridge and the breech face, the cartridge will stretch lengthwise when fired, thereby creating a dangerous situation in which the case may rupture and vent hot gas back towards the shooter.

A taper crimp is easy. The biggest problem that new taper-crimpers face is applying too much crimp. All that’s really necessary is to apply just enough crimp to remove the belling from the cartridge case after a bullet is seated. Think of a proper taper crimp as just making the walls of the case straight and parallel again.
For other cartridges, like revolver calibers such as .38 Special, .357 Magnum, and .44 Colt, to name a few, crimping can do more than just remove the “flare.” Known as “roll crimping,” this process can be used to push the edge of the brass case mouth into the bullet itself, helping lock it into place.
Last but not least, inspection!
The very last step in the process is inspection and packaging.
After all is done, I combine the inspection and packaging steps. As I put each completed cartridge into a box, I look it over to make sure everything is in order.
This is your last chance before your reloads head to the range to identify any problems, so make this an important part of your routine. If you see any issues, or even have doubts about a specific cartridge, remove it. You can use a bullet puller to take it apart and start over.
One more thing—the very last step. Go shoot it!
Tom McHale is the author of the Insanely Practical Guides book series that guides new and experienced shooters alike in a fun, approachable, and practical way. His books are available in print and eBook format on Amazon.
