Building with the Best: Making an AK with Definitive Arms
Matt Korovesis 12.08.15
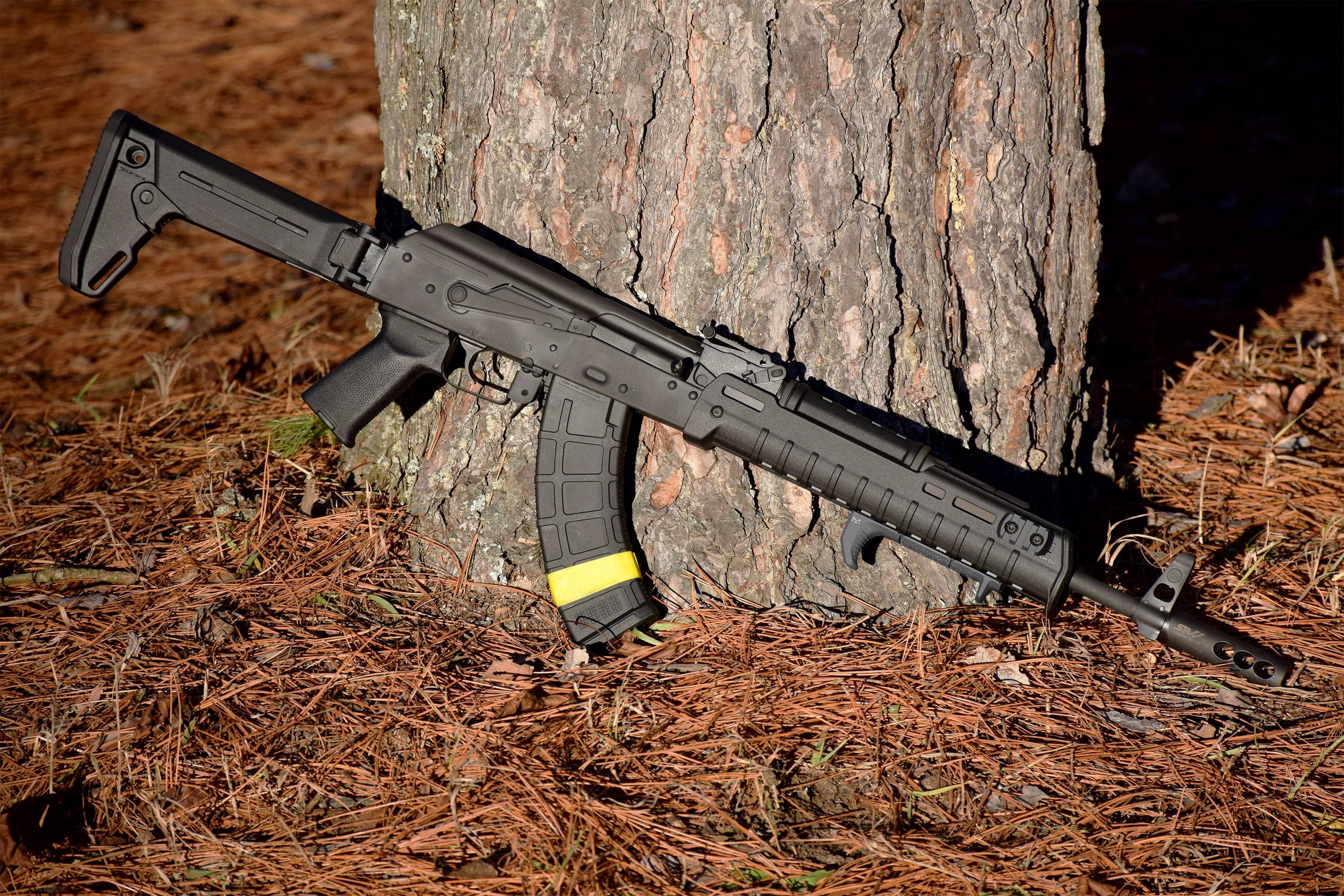
Definitive Arms is part of the AK Holy Trinity in the United States. Alongside Krebs Custom Guns and Rifle Dynamics, they’re considered the top dogs in American Kalashnikov manufacturing and customization. After October’s Big 3 East event, I was offered the tremendous opportunity to assemble my own AK in a small, hands-on build class. I was also able to get a glimpse of the tremendous amount of time, care, and knowledge that goes into each Definitive Arms gun.
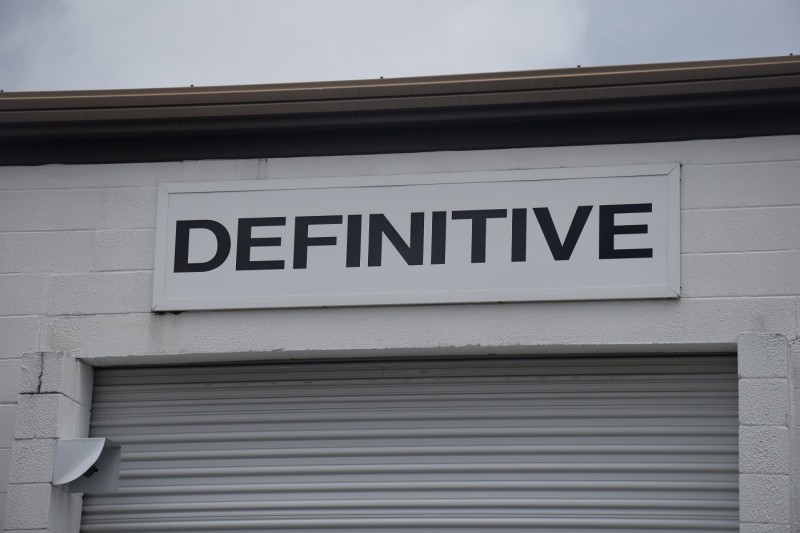
The DA shop is located not far from the freeway in an industrial part of St. Petersburg, Florida. A plain white sign with the text DEFINITIVE in bold black letters is the only indication an outsider might have that some of the most impressive gunsmithing in the United States is taking place inside.
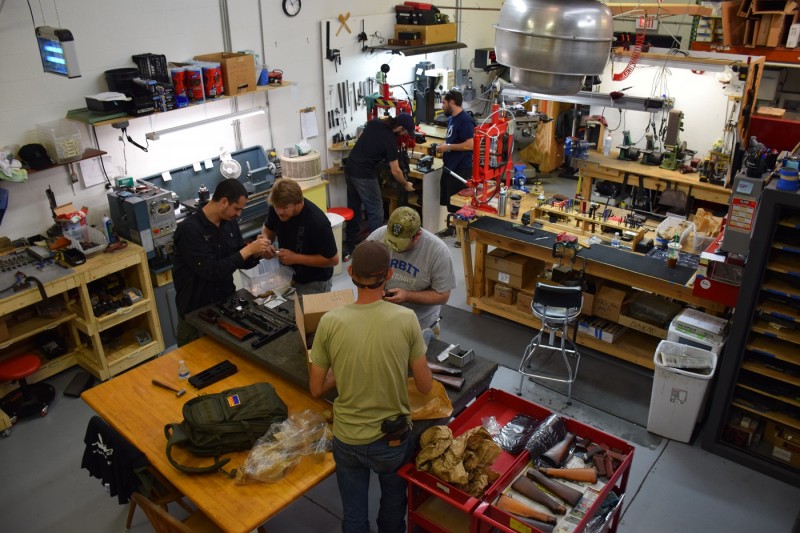
My classmates were Scot Hoskisson, the owner of RS Regulate, and Rich Elliott, a Marine veteran and professional firearms trainer who offers courses through his website, MarksmanshipTrainer.com. Tim Yan, a freelance writer, photographer, and Marine veteran, later joined us to photograph the endeavor. The DA crew that greeted us included Chase, the founder of Definitive Arms; Chase’s father (and DA financial handler) Gary; three of DA’s experienced staff (Zak, Karl, and Jimmy); and one adorable Basenji-Terrier shop dog named Monte.
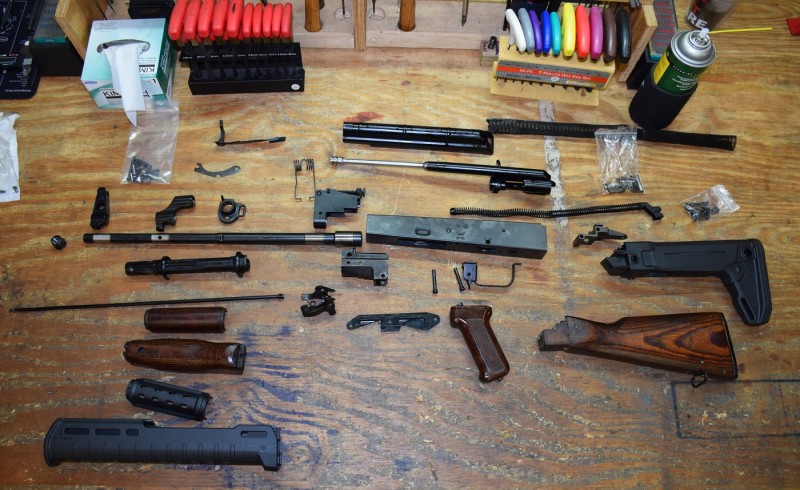
Our class projects were boxed up and ready for us when we walked in. The current run of DAKMs, Definitive’s popular AKM clone, are built using Polish parts kits, American Morrissey receivers, and American 4150 CMV barrels. According to Chase, Morrissey receivers are quite similar to original Russian military-grade receivers in regard to heat treatment standards and other properties, making them ideal building blocks for high-quality rifles.
The kits that Chase pulled for us were, like all other kits used for DAKMs, in great shape. Mine appeared to have come from a nearly-unfired rifle. Though our builds would not be built to exactly the same standards as production DAKMs (they couldn’t show us all their secrets), our guns would end up looking quite similar to them.
The kits for our class guns dated to the 1960s. Chase, in an informative side note that characterized our time spent in the shop, explained that he preferred the Polish parts from the ‘60s for some builds. The trunnions from that period tend to be particularly well-made.
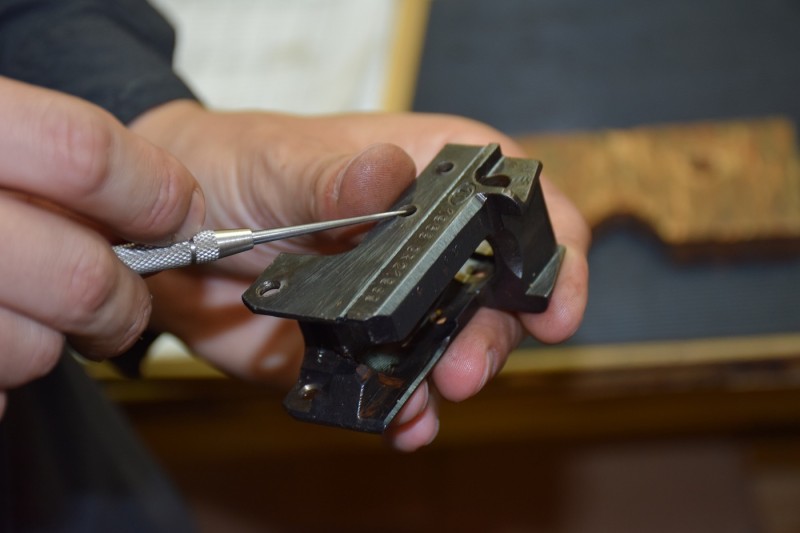
After laying out each of our unassembled kits for pictures, we embarked upon the first step of our builds: a detailed, part-by-part inspection—including the individual components of the bolt. Chase pointed out specific areas of each component that need to be examined in-depth and described how, where, and why they wear and break. This process can be time-consuming, but it’s critical. Other AK manufacturers breeze through it, and let consumers deal with the consequences.
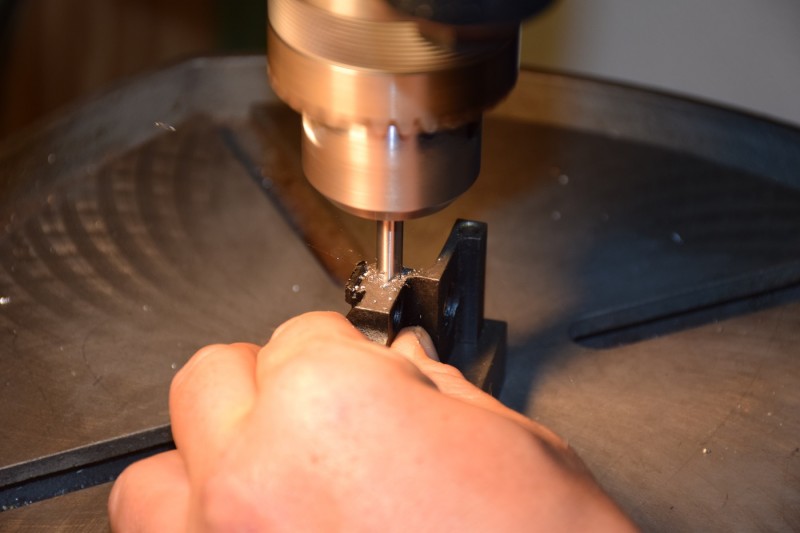
Following the inspection, we honed and chamfered our front and rear trunnions’ rivet holes. We then drilled the receivers for the trunnion and scope rail rivets. During the drilling and throughout most of the build, we used a Bridgeport mill equipped with a digital readout. The mill is capable of repeatable accuracy down to 0.0005 of an inch, or about one-eighth the thickness of an average piece of paper. Definitive avoids using receivers with pre-drilled holes whenever possible.
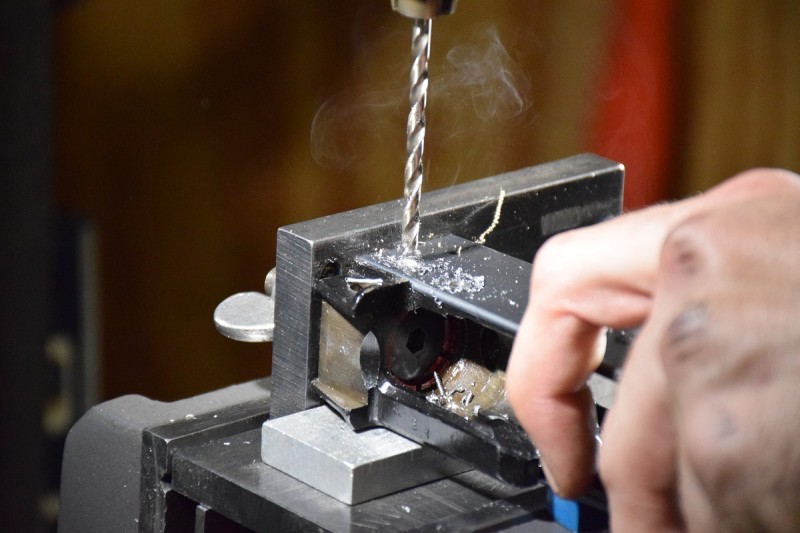
Next, we riveted the rear trunnion, scope rail, and front trunnion into the receiver while being guided by a member of the DA team. The consistent and precise machine work that Definitive Arms pours into their guns is a critical part of making an AK shoot accurately—many parts of an AK wobble, shake, and shift when fired. If those parts don’t return to the exact spot they were at, then the gun won’t be accurate. Many less-reputable manufacturers are content to rivet their AKs haphazardly, which can lead to serious mechanical and accuracy issues.
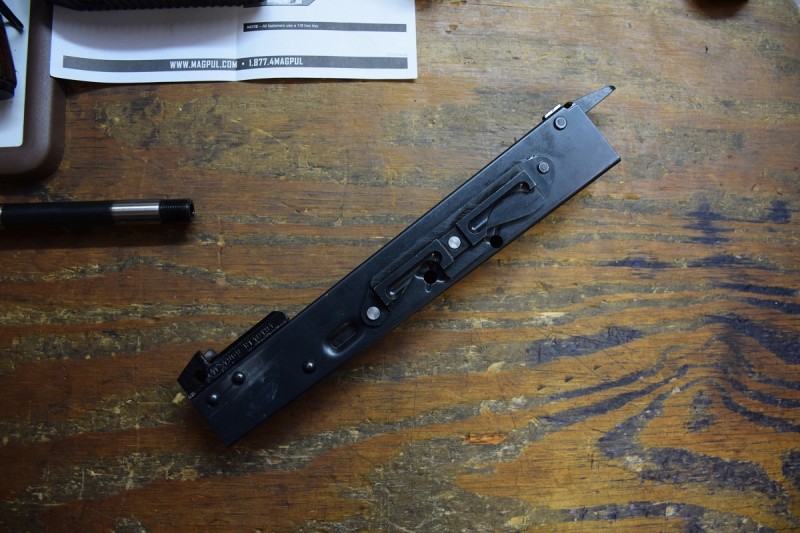
After getting the rail and trunnions riveted, we moved on to pressing our barrels into our guns’ receivers. This requires a great deal of finesse—otherwise, one may over-insert their barrel or leave it dangling out of the front end of the receiver. Following the installation of the barrel, we headspaced our guns with go gauges, no-go gauges, field gauges, and live cartridges to determine whether our bolts would properly lock up. This is another point that shoddy builders can brush past, resulting in dangerously out-of-spec AKs.
To save time, many manufacturers pre-assemble their barrels before pressing them in. Definitive presses them in stripped and installs the additional components one by one to ensure each piece is trued to the action. It takes longer to do, but results in a better, straighter, and more accurate AK.
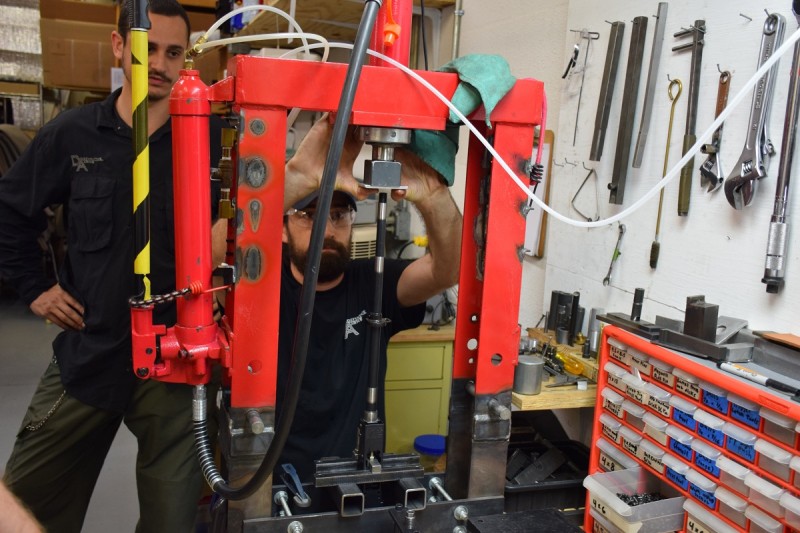
We then drilled and reamed our builds for insertion of the barrel pin. The barrel pin helps secure the barrel to the trunnion and receiver. We hammered our pins in with gusto, likely to the delight of any Soviet ancestors looking down upon us.
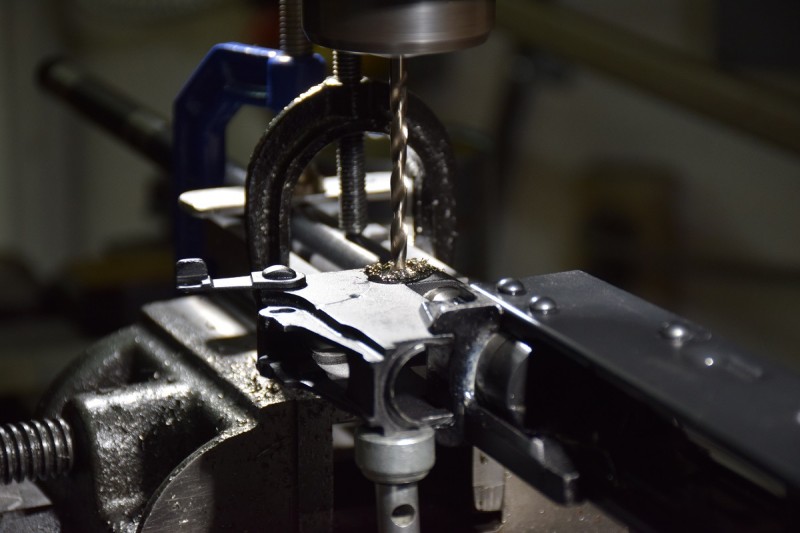
Next, we pressed on our rifles’ rear sight bases. After pressing the base on in a process similar to that of the barrel, we checked to make sure our dust covers fit properly. Chase then inspected each of our rear sight bases’ position relative to the front trunnion and receiver. A properly-fitted rear sight base will be level and squared to both. A skewed base will, obviously, lead to canted sights. Following this procedure, we went back to the Bridgeport to drill and ream the bases for another pin, which we also hammered in.
At this point, Rich and Scot slipped their handguard retainers onto their barreled receivers. As I was using a Magpul Zhukov handguard, which requires removal of the retainer from complete guns, I opted to simply leave it off during the build process.
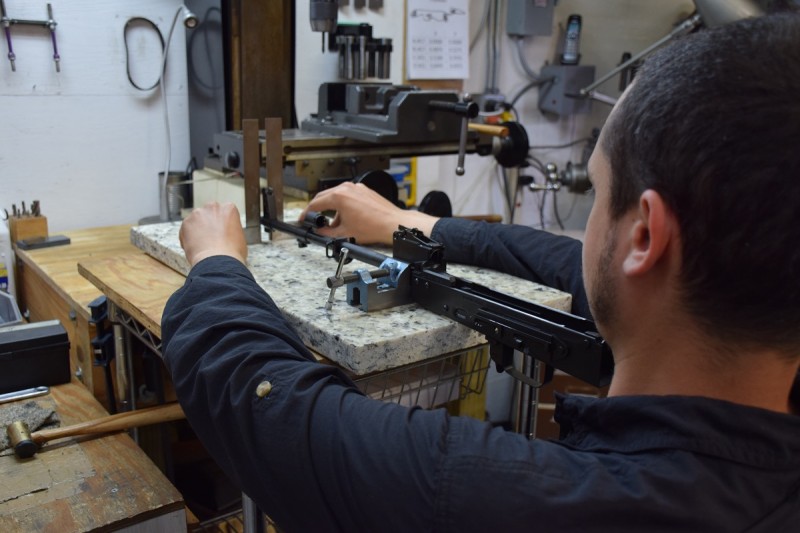
We then pressed on the gas block, followed by the front sight base. We squared both to the rear sight base, front trunnion, and receiver as best we could, then handed our projects over to Chase for final alignment. The “final squaring” of the sights and gas block is a process that Chase handles personally for most Definitive Rifles. It involves using a level surface, several vices, and two squaring brackets. Using a brass mallet when necessary, Chase ensured the front sight base, gas block, rear sight base, front trunnion, and receiver were as properly lined up and level as possible. Again, this is critical for ensuring the rifle’s sights are pointing where they should.
At this point, it was 11 p.m., and we decided to call it quits. We had been working on and off since 10 a.m.—on a Saturday, no less (though long, weekend hours are quite normal for the DA team). It turns out that it’s quite easy to get distracted and start talking about the finer and stranger points of Kalashnikovs when you toss nine people who obsess over them in a room together.
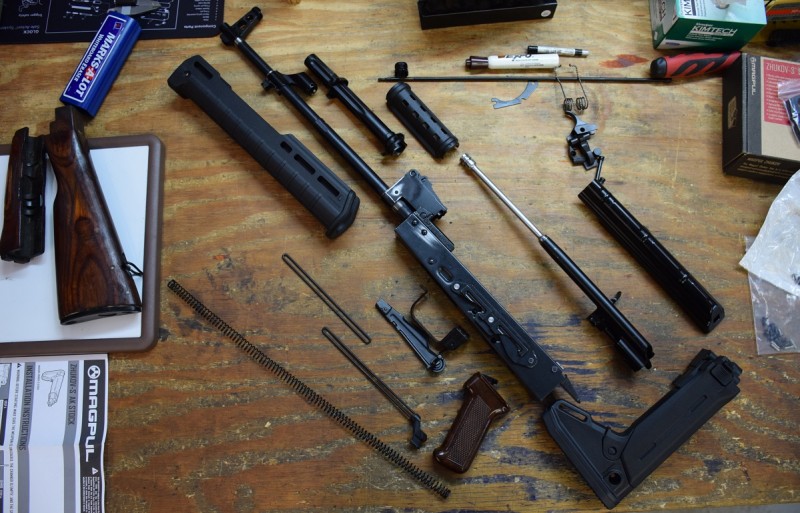
Nonetheless, we had been able to experience firsthand much of what sets Definitive Arms apart from lesser manufacturers. Precise and accurate machine work, extensive quality control, and hands-on tuning, fitting, and tweaking are just a few of those processes. Quite simply, Chase, Karl, Zak, Jimmy, Gary, and everyone else at Definitive Arms have an intimate knowledge of AKs and what makes them tick—and that shows in the reliability and reputation that are associated with DA guns.
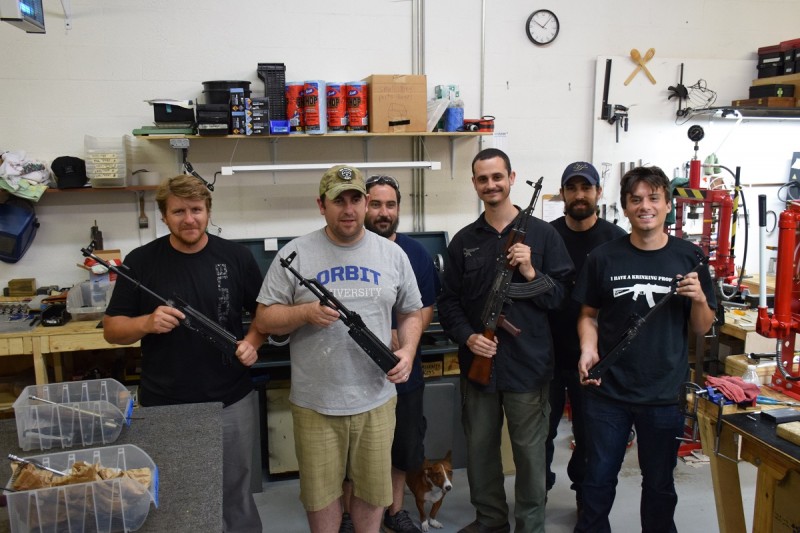
The main steps left to complete the build process were pinning the gas block and front sight base, riveting the trigger guard and magazine release assembly to the receiver, and tweaking the mag release to ensure compatibility with a wide variety of AK mags. The rifles would also be refinished in Definitive Arms’ usual black parkerization, laser-boresighted, and test fired.
I received my completed rifle from DA not longer after my build class. During the course of inspecting and dry-firing it, I came to the conclusion that it had one of the smoothest actions of any AK I’ve ever handled. I also quickly noted that DA’s parkerized finish was a huge improvement over the Eastern European “mil-spec” black paint that scratches away easily. In early December, I was finally able to take it to the range.
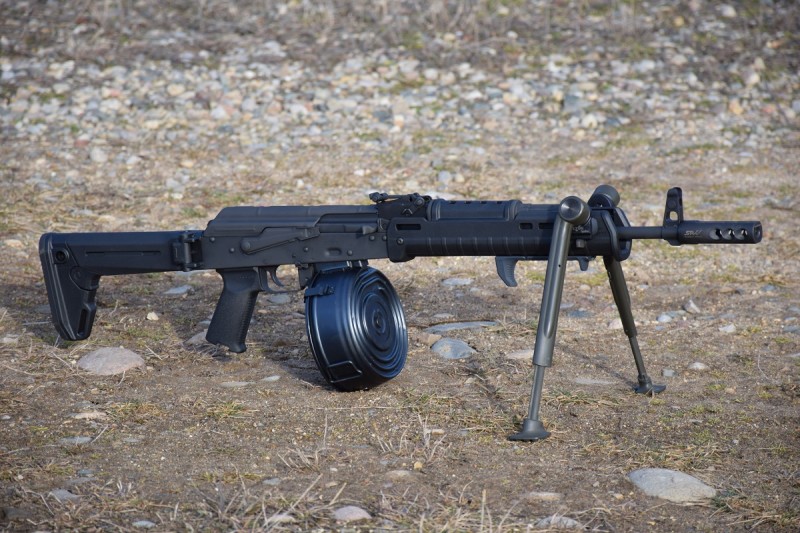
The benefits of Definitive’s time-consuming squaring process were immediately apparent. After blasting through 15 rounds as fast as I could at a close-range target to briefly check its function, I moved back to the 150-yard range. After firing a few “spotting” rounds at milk jugs lined up on a berm, I was able to pop jugs in quick succession over iron sights. For the remainder of the day, the rifle functioned reliably and sent rounds into the dirt with astounding precision. I eagerly look forward to getting thousands more rounds through the gun, but it’s plain to me that this rifle is going to be a regular part of my recreational and more practical shooting endeavors for many years to come.
My experience at Definitive Arms is not one I will soon forget. I walked away from the shop with a newfound appreciation for the men and women who dedicate themselves to building some of the finest AK rifles in the United States day after day.
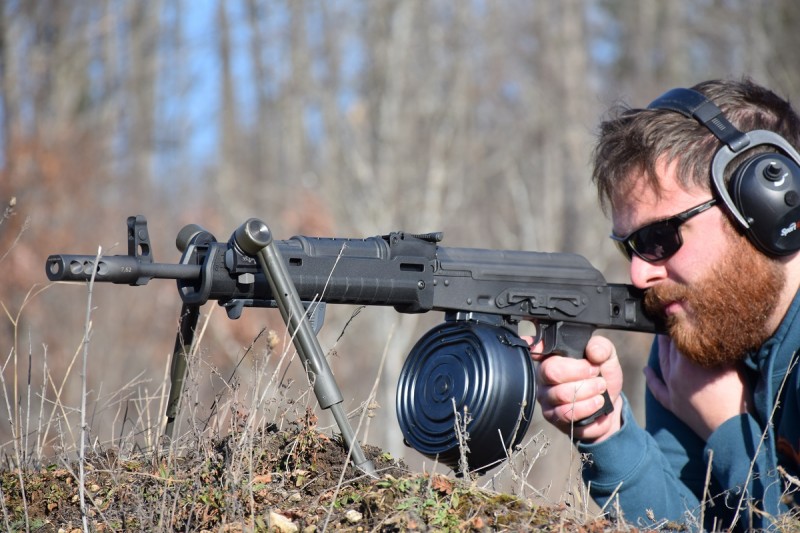
The passion that each DA employee has for their work is immense. With all of the Kalashnikov-related information stored in his head, I am amazed that Chase is still able to remember how to walk. Every firearm that leaves his facility is a hand-tuned piece of AK art. Companies like Definitive Arms prove that the application of American ingenuity and craftsmanship can elevate and evolve even the most “basic” of tools into something a step ahead of the pack.
If you’re interested in some of Definitive Arms’ custom work, check out my recent article on their experimental 6.5 Grendel Vepr rework. They will soon be updating their website to allow customers to plan out and submit custom builds. The company also recently began offering their Fighter Brake for sale, which has been very well-received by the AK community. Their rifles are typically available through Atlantic Firearms, though they sell out very quickly.
