A BLACKHAWK! Factory Tour: The Making of Holsters, Gun Stuff, and More
Tom McHale 09.17.13
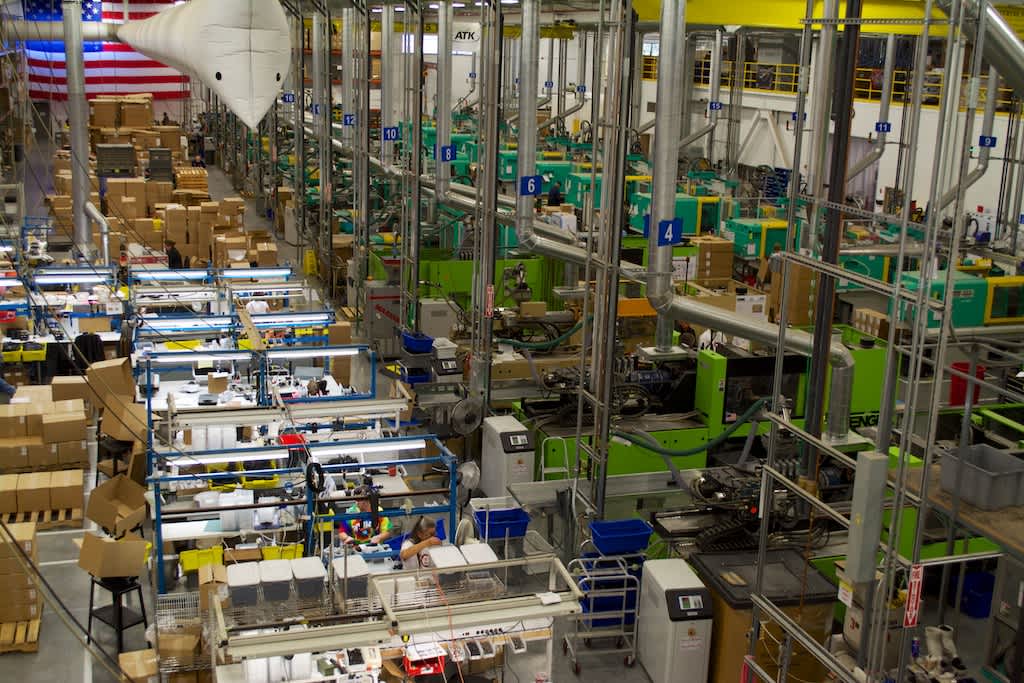
Last week I had the good fortune to tour the BLACKHAWK! manufacturing facility just outside of Bozeman, Montana. This isn’t just an assembly or packaging facility, it’s a soup-to-nuts, raw materials-to-finished product plant. Polymer beads come in one end, and really nifty gun parts and accessories come out the other.
Rather than blather on about how neat the BLACKHAWK! factory is, let’s take a photo tour:
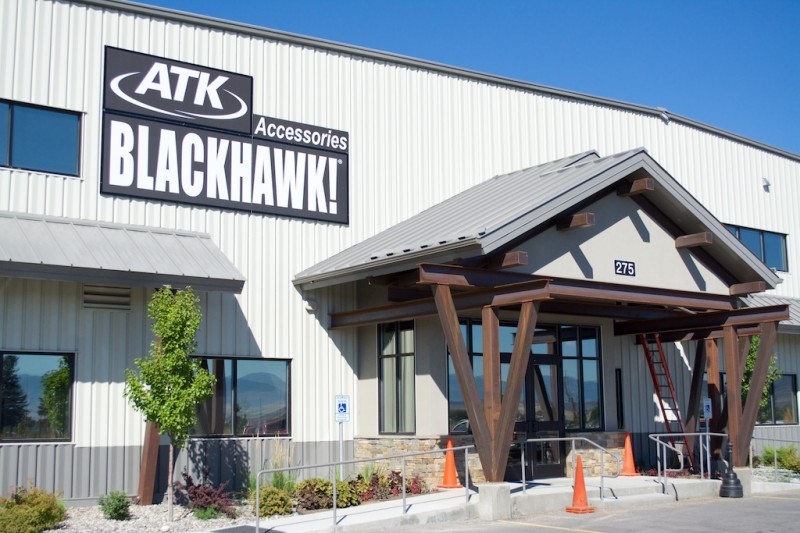
