Photos: On the Timney Triggers Factory Floor
Tom McHale 09.30.14
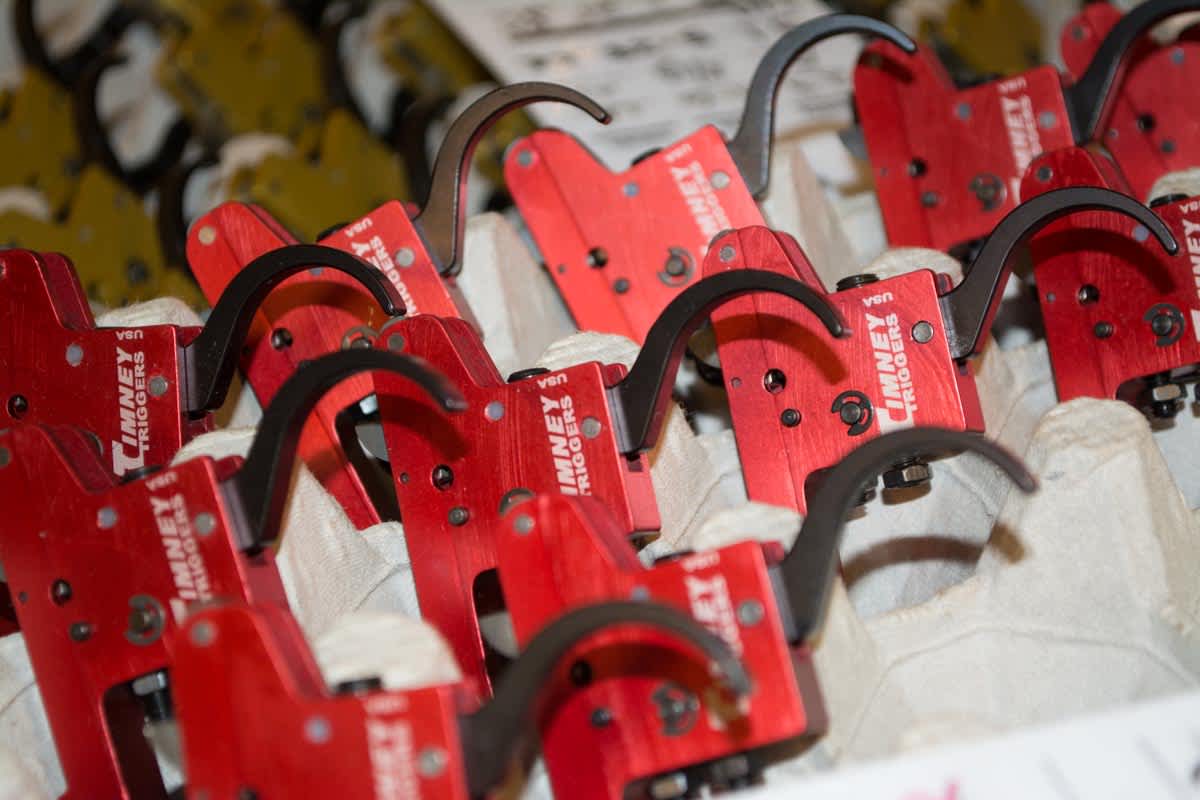
If you’re in the business of eking every last bit of performance out of an already fine-tuned product, you need a relentless (bordering on obsessive) sense of attention to detail.
Looking at the factory floor of Timney Triggers, the company’s compulsive behavior quickly becomes apparent. I’m sure you’ve heard the phrase “you could eat off the floor” before. At Timney Triggers, you really can. Well, actually you can’t, because eating off the floor would get it dirty. This place is seriously clean and polished. Even the brass outlet covers and ventilation grates on the factory floor are shiny. I suspect even a Marine Corps Drill Instructor would have to begrudgingly express satisfaction.

According to Timney Triggers owner John Vehr, this fanatical approach to organization and cleanliness sets the tone for the level of detail that goes into Timney’s product design, manufacture, testing, shipping, and, most of all, service. After all, he wants Timney to be known not for products and inventions, but their service. “I want Timney to be the Kleenex of triggers, so people say ‘Check out my Timney’ instead of ‘Check out my trigger,'” John says. The company intends to get to that point by removing internal competition and focusing all efforts externally. Every one of Timney’s 22 employees signs posters on the wall that detail Timney’s five commitments and Collaborative way. The fact that Timney has virtually no turnover seems to indicate their “corporate culture” is working.
I recently had the pleasure of spending a day touring the (relatively) new Timney manufacturing facility just north of Scottsdale, Arizona to see just how Timney trigger parts and assemblies are made. Hint: it’s a fascinating process which is a lot different than you might imagine. Let’s take a look.

The process starts in the spacious work area/lab/office/studio occupied by mad scientist Calvin. New gun candidates for Timney aftermarket triggers are racked up near Calvin’s desk awaiting scanning with a three-dimensional video imaging system. This captures exact dimensions of the internal receiver space that a potential Timney trigger has to occupy.

From our observations, Calvin seems to combine a mixture of engineering and art with hours, weeks, or even months of pondering design possibilities to figure out optimal solutions. The day we were there, Calvin was still contemplating design options for a replacement trigger for AK-type rifles. While he had partially-functional prototypes, it’s still unclear as to whether Timney will ultimately market the product. In the case of AK triggers, the market demand is there, but getting something to be universally compatible with the wide variety of AKs available is proving difficult.

Once a design is finalized, production starts using a dizzying array of high-tech automation. One thing you won’t see at Timney is a bunch of people working mills and lathes. Timney has heavily invested in technology for consistency and economies of scale. On the factory floor proper, we only saw one person on the manufacturing floor monitoring and configuring machines. According to Vehr, it would take somewhere in the neighborhood of 60 factory workers to produce the same level of output as Timney’s highly automated shop.

The workhorses of the manufacturing floor are three-part robotic systems. An automated conveyor feeds steel or aluminum blocks via conveyor to a robotic arm system. The robot feeds and orients components for a robot-drill milling system, which then shapes and cuts metal parts. It’s mesmerizing to watch.

When cutting hard raw material like A2 steel, drill bits like these need to be changed twice a day. When working on aluminum components, the replacement frequency is about once per month.

Most of the actual trigger faces are cut with wire EDM (electrical discharge machining) devices. It’s a spark-cutting process that I’m pretty sure is the same technology that Dr. Frankenstein used to bring his monster to life.

In overly simplified terms, these machines feed a thin wire through small holes in the steel plates automatically. Massive electricity is applied while the steel plates are submerged in a dielectric solution. The end result of the electro-magic is a bunch of triggers in a bin—and really cool-looking steel plates with cutout shapes.



Other components, like Ruger 10/22 latch plungers, are cut with more traditional (but still fully-automated) milling machines.


More humans enter the picture at the assembly and testing phases. Completed parts from the factory floor head to an assembly and testing room where components are assembled into working trigger systems. Some are simple, while other assemblies, like the Timney Triggers Ruger 10/22 system, require careful assembly of dozens of different parts.

Once trigger groups are assembled, they’re placed into large egg crates to await testing. Watching technicians test the triggers is an observation of zen. Most of the function testing is done by feel, with constant adjustments and retesting done with little need for a look. Of course, final trigger weight testing is done with a trigger scale to ensure a precise adjustment.

The testing shop maintains a rack of barreled, partial actions that can be clamped into a vise so each and every trigger is manually tested in an actual gun action.




Once triggers are machined, hand-assembled, and hand-tested, they’re off to be shipped. The number of completed triggers we saw moving through the system was staggering considering we were only there for a single day. AR-15 replacement triggers are the hot item now, but Timney offers replacements for dozens of other rifles including the Ruger 10/22, Remington 700, Mosin-Nagant, Arisaka, Browning A-Bolt, Tavor, and various Mausers, Springfields, Savages, and Winchesters—just to name a few. Check the product section of the website for a full listing.
Why all this expensive equipment to produce triggers? That’s easy. While a perfectly built and adjusted trigger does not physically make your rifle more accurate, it does allow you to wring the maximum level of performance out of your rifle. In a recent field test, I shot a series of groups with a Daniel Defense 300 BLK build and a Rock River Arms 6.8 Remington SPC rifle. I then replaced the trigger with a Timney AR-15 Competition model while still at the range, and re-shot the same groups. The difference? On average, the five-shot groups shot after the trigger upgrade were two-thirds the size of the pre-upgrade rifles. Same guns, same ammo, same range, same conditions, same shooter. What a difference a good trigger makes!
Tom McHale is the author of the Insanely Practical Guides book series that guides new and experienced shooters alike in a fun, approachable, and practical way. His books are available in print and eBook format on Amazon.
