Designs for 3D-printable AR-15 Bullpup Lower Released
OutdoorHub Reporters 05.27.14
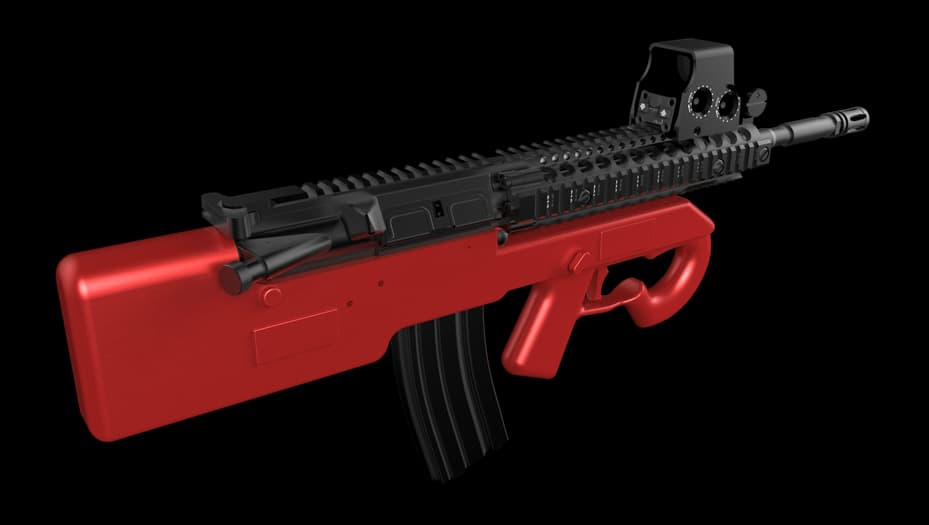
Roughly one year ago OutdoorHub reported on a design for a 3D-printed hybrid AR-15/FN P90 lower receiver known as the “Charon.” Recently, the amateur firearms designer behind the Charon released the blueprints for a unique lower that is rapidly drawing attention in the gun community.
“This is an AR-15 based bullpup. It is highly experimental,” wrote its elusive creator, who is known interchangeably as WarFairy and Shanrilivan.
Naming the new lower after the Hindu deity Hanuman, WarFairy announced the release of the lower on reddit last week. The files necessary to print the Hanuman are available at defcad.com, a website for designers and hobbyists created by 3D-printing pioneer Cody Wilson.
“After entirely too long of a development cycle, I give you the Hanuman AR-15 Bullpup,” WarFairy wrote in a reddit thread. “It is very much a prototype, lacking a safety and adjustable LOP (outside of interchangeable butt pads), but should work without issue.”
The designer noted that the current version of the Hanuman was made to test for ergonomics and general functionality. WarFairy expects that later versions will include a safety. As it is now the Hanuman lower requires a bufferless upper receiver to function, such as the ARAK-21, Rock River Arms PDS Carbine, or a normal upper with a CMMG-style .22 LR conversion. Like the Charon, the Hanuman’s individual pieces are designed to be printed separately, allowing those with smaller 3D printers to construct the device. ABS plastic is a relatively light and cheap material that holds up well to the pressure of firing live ammunition. WarFairy stated that test receivers have fired well over 600 rounds and are still functional, although they are now showing signs of stress.
“The entire lower weighs 1.45 pounds when created in ABS, so material cost will be between 20 and 40 dollars depending on the cost of your material,” WarFairy wrote.
Designers like WarFairy say they are drawn to 3D printing because of what the technology is capable of. Perhaps the most visible benefit of using a 3D printer over more traditional production methods is that a prototype can be built in mere hours instead of days or weeks. Changes can be practically made on the fly, and designs can be released to the public for scrutiny, criticism, and improvement.
“No design exists in a vacuum, and having multiple eyes on it always shows things that the designer can’t see,” WarFairy wrote.
